OMSLAGARTIKEL
BENCHMARK IS IJKPUNT VOOR PRESTATIEVERBETERING + VERGELIJKEND ONDERZOEK NAAR HONDERD EUROPESE PRODUCTIEBEDRIJVEN + 80 % PRODUCTIEKOSTEN WORDT VASTGELEGD IN ONTWERPPROCES
Ingenieurs brengen goeroedom naar de werkvloer
Managementhypes vertaald
in bruikbaar gereedschap
Het vertalen van goeroewijsheid over trends zoals lean production en business process redesign (BPR) is vaak net een stap te ver voor managers in de industriële productieomgeving, vooral in het midden- en kleinbedrijf. Dagelijkse beslommeringen eisen alle aandacht op. Grote adviesbureaus hebben echter methoden ontwikkeld om de nieuwe organisatieconcepten te concretiseren voor specifieke productiesituaties.
– Erwin van den Brink –
De auteur is redacteur van De Ingenieur.
De tijd van de grote managementhypes van de jaren tachtig en negentig is aan het overwaaien. Terwijl de orakeltaal van goeroes zoals Tom Peters en Michael Hammer nog nagalmt, zijn de ingenieurs Mat de Vaan en Maurits Verweij (Berenschot), Rufus Udo en Remco Overwater (Andersen Consulting) met het down to earth-monnikenwerk begonnen om de verlichte ideeën te engineeren tot gevalideerde, gestandaardiseerde methoden die direct in de bedrijfspraktijk toepasbaar zijn.
Het adviseren heeft zich daarmee verplaatst van ons nachtkastje – waar de boeken van Drucker, Peters, Hammer en Jones al dan niet gelezen liggen – naar de werkvloer. Trends zoals lean production (Jones) en business proces redesign (Hammer) hebben inmiddels hun sporen nagelaten in grote bedrijven in de auto-industrie en de (zakelijke) dienstverlening. Hiervan afgeleide methoden sijpelen nu door in kleine industriële ondernemingen en beogen de prestaties te verbeteren van bepaalde bedrijfsfuncties zoals de productontwikkeling. Wat deze methoden gemeen hebben is hun praktische toepasbaarheid.
Onderzoeksschool Beta
De adviessector boort steeds meer specifieke marktsegmenten aan. De Twents-Eindhovense onderzoeksschool Beta stelt informatica centraal bij het herzien van bedrijfsprocessen, terwijl TNO in het programma ‘Modern produceren in het MKB’ een hele reeks aan (bestaande) technologieën en methodologieën (varirend van cadcam tot just in time) heeft aangepast aan de praktijk van kleine bedrijven.
Dit jaar hoopt ir. Maurits Verweij van adviesbureau Berenschot uit Utrecht te promoveren op een proefschrift waarin hij de mogelijkheden onderzoekt om de kennis van de grote onderzoeksinstituten zoals TNO en de universiteiten toegankelijker te maken voor het MKB. Tot het MKB behoren volgens de Europese Unie alle bedrijven met minder dan 250 medewerkers, een omzet van minder dan veertig miljoen ecu (f 86 miljoen) die voor minder dan een kwart eigendom zijn van een groot bedrijf. Doorgaans komt nieuwe kennis voor dergelijke bedrijven van de klanten en toeleveranciers. Waar moeten zij beginnen om hun kennishorizon te verbreden?
Verweij: ‘Nodig is een eenvoudige, goedkope methode om een snelle diagnose te stellen van de eigen productieorganisatie.’ Kleine ondernemers kunnen het zich immers niet veroorloven om met hun personeel een week op de hei te gaan zitten: wie neemt dan de telefoon aan?
Daarom heeft Berenschot samen met het de TU-Eindhoven, de universiteit van Hannover en het Duitse adviesbureau Kienbaum in het kader van het Europese onderzoeksprogramma Brite Euram II een methode ontwikkeld voor het herontwerpen van het productieproces bij kleine en middelgrote bedrijven die actief zijn in enkelstuks- of kleinseriefabricage. Een vorm van BPR die praktisch te hanteren is voor kleine industriëlen. Reorganiseren met beide benen op de werkvloer.
‘We wilden de drempel verlagen voor middelgrote en kleine bedrijven’, zegt prof.ir. Mat de Vaan van Berenschot. ‘De algemene methodiek BPR is eigenlijk helemaal toegesneden op de dienstverlenende, informatieverwerkende bedrijven en niet op de industriële productie, laat staan op de kleinschalige productie.’
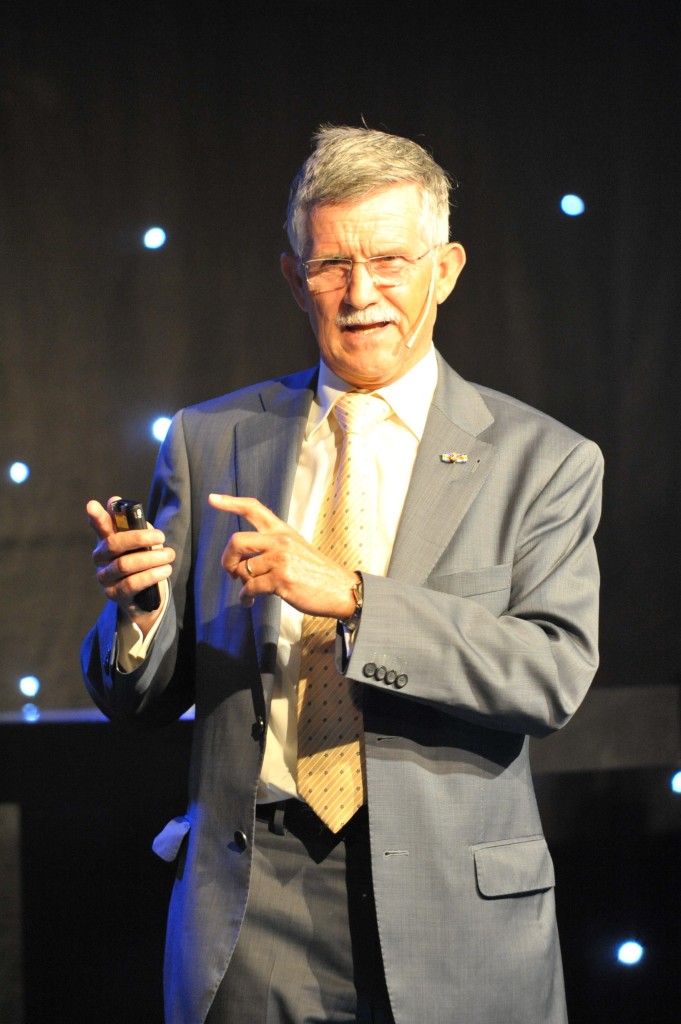
Centraal in de Berenschotmethode die HOPE heet (Human Oriented Production Engineering), staat de zogenoemde Production Description Language (PDL). Deze taal (zie kader) beschrijft de optimale productieorganisatie voor een bepaald werkstuk of product in termen van bekende basistypen zoals de assemblagelijn, stationaire samenbouw (in een dok of op een platform), een mobiel assemblageplatform en de productiecel of taakgroep.
PDL wordt niet alleen gebruikt om de optimale organisatie van de productie te bepalen, maar is tevens een instrument voor benchmarking. In vervolg op het HOPE-project neemt Berenschot momenteel deel aan benchmarking van honderd productiebedrijven in Duitsland, Zweden, Groot-Brittannië, Spanje en Italië. Dat gebeurt in het kader van het Europese Betti-project (Benchmark Tool To Improve The Production Performance), onderdeel van het nieuwe Europese technologieprogramma Innovation. Doel hiervan is het creëren van een database met Europese productiegegevens. De prestaties van de onderzochte bedrijven worden bij benchmarking ten opzichte van elkaar geijkt. Daarmee kunnen bedrijven snel meten hoe zij het doen ten opzichte van vergelijkbare bedrijven in Europa.
Productontwikkeling
Ook Andersen Consulting uit Eindhoven heeft recentelijk het nodige gedaan aan benchmarking. Dit wereldwijd opererende bureau richtte zich daarbij niet op een bepaalde categorie bedrijven maar op een bepaalde bedrijfsfunctie, namelijk de productontwikkeling of engineering. ‘Na de hausse van verbeteringen in het logistieke proces wordt langzaam duidelijk dat de weg naar verdere verbetering van de concurrentiepositie loopt via het ontwerpproces’, stellen dr. ir. Remco Overwater en ir. Rufus Udo in een publicatie van Andersen Consulting. Dit bureau deed in de VS een benchmark-onderzoek naar het engineering-proces van tien grote industriële productiebedrijven, recent gevolgd door een benchmark-onderzoek in vijf Nederlandse productiebedrijven. Uit dat onderzoek komt naar voren dat de situatie in grote industriële bedrijven in de VS en in Nederland niet dramatisch verschilt: in beide landen valt nog een hoop te verbeteren. In de VS is men over het algemeen verder met interne gegevensuitwisseling (bedrijfs-automatisering) en wordt eerder gekozen voor technische oplossingen, terwijl Europese ondernemingen eerst kijken naar de organisatie: dat geeft snel resultaat en hoeft niet veel geld te kosten. Toch zijn goed beheer van product- en procesgegevens en efficinte uitwisseling van zulke gegevens binnen bedrijven en tussen samenwerkende bedrijven de grote problemen die in Europa de komende jaren moeten worden opgelost. In toepassing van informatica hebben wij een achterstand op de Amerikanen.
In dit verband adviseerde Andersen Consulting de laatste tijd een aantal bedrijven in de machinebouw over een verkorting van de doorlooptijd van hun ontwerpproces (‘engineering’).
Re-engineering, het herontwerpen van bedrijfsprocessen, nam in de productieomgeving al snel de gedaante aan van lean production: zonder voorraden (just in time leveren van onderdelen) en zonder wachttijden produceren. Dat had veel te maken met het verbeteren van de logistiek. Nu sijpelt het herontwerpen van processen steeds meer door naar de engineering-afdelingen.
‘Engineering is erg traditioneel en van oudsher een machtig bolwerk binnen het bedrijf’, zegt ir. Remco Overwater die voor Andersen Consulting een aantal re-engineering-projecten deed. ‘De ingenieur die daar zit is zeer gehecht aan hetgeen hij nodig heeft om creatief en goed bezig te zijn. Hij hanteert vaak zijn eigen doelstellingen. Ontwerpers zijn bijvoorbeeld geneigd de kwaliteit van het ontwerp te verbeteren ten koste van de tijd die nodig is om het product te vervaardigen.’
‘Tachtig procent van de productiekosten wordt bepaald in het ontwerpproces’, licht zijn collega ir. Rufus Udo toe. Hij noemt als voorbeeld een machinefabriek waar Andersen Consulting over de vloer is geweest. ‘Een machine die voor negentig procent uit eerder ontworpen of standaardonderdelen bestaat, werd toch telkens voor honderd procent ge-engineerd. We hebben daar modulaire ontwerpen ingevoerd, waarbij je met een vaste set van verschillende modules machines kunt bouwen die aan alle specificaties van de klant voldoen zonder dat de constructie-afdeling er nog aan te pas komt. Dat werkt zo fundamenteel anders dat het veel tijd kostte ingenieurs te overtuigen. Op dit moment zijn ongeveer tien van de dertig machine-ontwerpen gemodulariseerd. De mentale barrière is echter overwonnen zodat we moge verwachten dat de modularisatie van de overige ontwerpen in een fractie van de tijd wordt gerealiseerd die het tot nu toe heeft gekost.’
Nieuwe generatie
‘Doordat ingenieurs zich veelal richten op het engineeren van orders, in feite het aanpassen van bestaande ontwerpen voor nieuwe klanten, schiet de ontwikkeling van geheel nieuwe producten er bij in en terwijl de ingenieur daar juist waarde aan kan toevoegen. Nu zie je alleen maar zeer incrementele productontwikkeling; een machine blijft in grote lijnen twintig jaar hetzelfde, er is geen tijd om een nieuwe generatie te ontwikkelen.’
Wat geldt voor engineering geldt vooral in kleine industriële bedrijven. Zoals de constructie-afdeling van bedrijven in enkelstuks- en kleinseriefabricage is gespitst op het ‘engineeren van orders’ zo is ook de productie gericht op het ‘op tijd de deur uit krijgen’. Bedrijven hebben het druk met het hoofd boven water te houden.
De Vaan: ‘We leven in hoge-loonlanden. Om te kunnen blijven concurreren moet je alles uit de productieorganisatie halen wat er uit te halen is. Moderne apparatuur, automatisering, is wel een voorwaarde, maar biedt niet voldoende soelaas. Automatisering en productieorganisatie waren toch twee aparte werelden. Daarom wilden wij een alomvattende methodiek maken die de technische én de menselijke aspecten beschrijft.’
‘Stel: een bedrijf twijfelt tussen optimaliseren van de productie en verhuizen naar een lage-loonland. De eerste stap een in onze visie is dan: doe een benchmark. We zijn nu in staat op een workshopachtige manier tot een zeer snelle analyse te komen. We kunnen de productie binnen verschillende bedrijfsonderdelen snel typeren en de totale performance van een bedrijf in kaart brengen. Er zijn internationaal kengetallen beschikbaar over bijvoorbeeld assemblagebedrijven die betrekking hebben op de bewerkings- en doorlooptijd. Als kengetallen dan niet worden gehaald, weet je vaak dat het ligt aan een suboptimale productieorganisatie van bepaalde bedrijfsonderdelen.’
Concurrent engineering
‘Benchmarking is een inderdaad een vertrekpunt’, bevestigt Overwater. ‘Vervolgens kun je zover gaan dat je niet alleen je bedrijfsprocessen herontwerpt, maar dat je de hele business herdefinieert, abstraheert, waardoor je bijvoorbeeld overeenkomsten ziet ontstaan tussen het ontwikkelen van een zaktelefoon en een auto. Zo kun je daar als automaker ook wat van opsteken.’
Een goede consultant spaart daarbij ook zichzelf niet. Udo: ‘Ook wij zijn voortdurend bezig te zoeken naar mogelijkheden de doorlooptijd te verkorten van onze eigen projecten bij klanten. We ontwikkelen daarvoor methodologieën waarin aspecten zijn verwerkt van concurrent engineering. Een van de initiatieven in dit verband noemen we re-inventing systemsbuilding.’
‘Concurrent engineering, waarbij je tegelijkertijd met een product samen met alle betrokkenen – klant, Marketing & Verkoop, Inkoop, leveranciers, engineering – de daarvoor benodigde processen ontwerpt, komt uit een heel andere wereld. Ook dát is een vorm van benchmarking, het vergelijken en ijken van processen. En dan krijg je wat re-inventing the business wordt genoemd: soms ontkom je er niet aan de kernactiviteit te herdefiniëren, te greenfielden, om helemaal out of the box, los van alle bedrijfsbeslommeringen, buiten de gebaande paden, je af te vragen wat je competence is waarin je bedrijf zich in essentie onderscheidt van andere bedrijven.’
Harley Davidson
Zo herdefinieerde motorfietsenfabrikant Harley Davidson onder de hoede van Andersen Consulting zijn business als een bepaalde, vrijgevochten levensstijl. Je hebt motorrijders en Harley Davidson-rijders. Eerst moest natuurlijk de Japanse concurrentie worden geëvenaard door de grote hoeveelheid foutproducten uit te bannen. Dat betekent reworking en terugdringen van de inefficiëntie in de productie (grote voorraden, laag productietempo, lange wachttijden, veel onderhanden werk en dus een groot kapitaalbeslag). Door lean te gaan produceren dus.
Maar vervolgens werd om Harley Davidson een nieuw imago opgetuigd. Bij de HD-dealers in de VS vindt de klant een kiosk met een pc waar je á la carte je eigen motorfiets kunt samenstellen: van kleur tot en met het motorgeluid. Udo: ‘Als een machine wordt samengesteld uit door engineering vrijgegeven, gevalideerde modules, is het niet meer nodig om met die order langs engineering te gaan.’
Ontwerpers zijn geneigd zich daar tegen te verzetten. Bij DAF-trucks is sprake van client driven engineering, waar een configurator, een computerprogramma, klanten in staat stelt een vrachtwagen volgens eigen wensen en eisen samen te stellen. De configurator geeft aan welke combinaties van modules wel en niet kunnen. Een configurator is het front end van het logistiek systeem; de productie en de inkoop van onderdelen wordt er mee aangestuurd. De configurator moet worden onderhouden vanuit engineering.
Met zulke methodologie en technologie hebben bekende producenten zoals Harley Davidson dus het Aziatische tij weten te keren. Hetzelfde geldt volgens Mat de Vaan voor kleine bedrijven die nu aan zet zijn: ‘Een Taiwanese fietsenfabrikant gaat hier in Nederland een fietsenfabriek opzetten, omdat hij dichter bij de markt wil zitten en zo sneller kan leveren. Tegenwoordig wordt de productiviteit meestal bepaald door de mens-machine-combinatie: als de bediener van een dergelijke machine een beetje doeltreffender gaat werken, verhoogt dat de productiviteit zodanig dat het loonkostenvoordeel van een lage-loonland in het niet valt.’
(FOTO 1
(BIJSCHRIFT )
Klanten van DAF kunnen, als zij een nieuwe vrachtwagen kopen, deze met behulp van een zogenoemde configurator geheel naar eigen wens samenstellen. (Foto: DAF)
(FOTO 2)
(BIJSCHRIFT )
Prof.dr.ir. Mat de Vaan (links) en ir. Maurits Verweij: …met een eenvoudige methode de drempel verlagen voor kleine en middelgrote bedrijven die hun processen willen verbeteren… (Foto: Michel Wielick).
(FOTO 3)
(BIJSCHRIFT)
Dr.ir. Remco Overwater (links) en ir. Rufus Udo: ‘Na de hausse van verbeteringen in het logistieke proces wordt langzaam duidelijk dat de weg naar verdere verbetering van de concurrentiepositie loopt via het ontwerpproces.’
(Foto: Michel Wielick)
(KADER)
Er is HOPE voor het MKB
De HOPE-methode van Berenschot beoogt niet zoals de aanpak van Andersen Consulting om in laatste instantie de eigen bedrijfsactiviteit, de business, te herdefiniëren en aan de hand daarvan het bedrijfsproces fundamenteel te herontwerpen. Bij fundamenteel herontwerp is het aangrijpingspunt al gauw de productontwikkeling, de ontwerpafdeling, omdat meestal daar het bedrijfsproces begint.
Het aangrijpingspunt van de HOPE-methode is het productieproces. Door het productieproces te herontwerpen aan de hand van (slechts) zes basistypen, wordt tijd en dus geld bespaard. Lean production en BPR veronderstellen vaak inzet van automatisering; informatica en robotica zijn dan dus duur en tijdrovend.
Ir. Maurits Verweij: ‘Voor het beschrijven van een productieomgeving kun je een aantal basisvormen onderscheiden. De problemen waar een bepaald bedrijf tegen aanloopt, zijn misschien te wijten aan een verkeerde grondvorm. Het gaat er daarbij om hoe ingewikkeld een product is, hoeveel exemplaren er van moeten worden gemaakt en welke eisen aan flexibiliteit worden gesteld. Daarbij moet je kengetallen waarderen in hun context: een serie van tien vliegtuigen is al heel wat, een serie van tien auto’s is niets.’
‘De autonome groep, manufacturing cell of Productions Insel, is een van die grondvormen ofwel basic types: een team maakt geheel zelfstandig een afgerond (onderdeel van een) product. Aan het andere uiterste van het spectrum bevindt zich de functionele afdeling, waar slechts een taak van een order wordt verwerkt waarna de order doorschuift naar een volgende afdeling. Daartussen ligt bijvoorbeeld het Flexibel Manufacturing System (FMS), de geautomatiseerde versie van de productiecel. Verder onderscheiden we de multiproductielijn en het stroomdok. Hierbij verplaatst het product zich nog wel serieel langs een assemblagelijn, maar op elk station werkt een groepje mensen aan parallelle taken. Ten slotte is er stationaire productie waarbij men voor uiteenlopende handelingen specialisten naar de ‘bouwplaats’ stuurt.’
‘Met suitability profiles, een waarderingsmatrix van verschillende productieaspecten zoals seriegrootte, productvariëteit, hoeveelheid onderdelen, aantal montagehandelingen e.d., geven we aan hoe in verschillende situaties verschillende grondvormen meer of minder geschikt zijn.’
Kort cyclische arbeid
HOPE neemt niet zozeer de technische mogelijkheden als uitgangspunt maar het aanwezige menselijke kapitaal en zoekt daarbij de beste technologische mogelijkheden. Een bedrijf kan voor een productieproces kiezen uit een taakgroep of een productielijn. Een dergelijke keuze hangt af van het opleidingsniveau of zelfs van persoonlijke voorkeuren.
De Vaan: ‘Niet alle mensen hebben dezelfde verwachtingen ten aanzien van hun werk. Je kunt dus niet zonder meer zeggen dat kort cyclische arbeid aan een assemblagelijn altijd voor iedereen vervreemdend werkt – alhoewel arbeid met extreem korte cycli, dus met een hoge mate van eentonigheid, voor niemand leuk is. Maar je zit uiteindelijk met economische randvoorwaarden.’
‘De productiesituatie is bepalend. Daarbij gaat het niet alleen om de aard van het product en hoe het geproduceerd moet worden, maar ook met het soort personeel. Voor een lijnproductie zijn andere mensen nodig dan voor productiecellen. In sommige situaties zijn productiecelachtige structuren en een assemblagelijn gelijkwaardige alternatieven.’
Het Duitse bedrijf Windhoff AG (machinebouwer van met name industriële transportmiddelen, 450 personeelsleden) was een van de drie bedrijven in het HOPE-project, samen met het Eindhovense bedrijf Frencken (onderdelen voor onder meer lucht- en ruimtevaartindustrie) en het Belgische bedrijf Verhaegen (fabrikant van bedden en lattenbodems).
De trend bij Windhoff is dat het productenpalet steeds groter wordt en de series kleiner. Dat leidde tot voorraadbeheer, interne logistiek, planning en besturing.
Toen HOPE bij Windhoff werd ingevoerd, waren net twee assemblagelijnen op elkaar aangesloten en optimaal geschikt voor het produceren van een groot aantal uniforme producten. Op een van deze lijnen werden twee verschillende soorten bouwmachines gemaakt: een met veel klantspecifieke onderdelen en een met minder klantspeficieke onderdelen. Omdat grote aantallen nodig waren van beide typen, werd de lijn beurtelings drie weken voor het ene en drie weken voor het andere type gebruikt. Dat betekende lange levertijden voor exemplaren van de afzonderlijke typen.
Besloten is de producten met speciale eisen voor de klant niet langer tussen het standaardproduct door op een lijn samen te bouwen, maar pas te monteren nadat het product de assemblagelijn heeft verlaten. Heeft een product heel veel klantspecifieke onderdelen dan wordt het stationair in een bouwdok geassembleerd. Kwaliteitsborging wordt gedaan door de productiemedewerkers zelf om zo de doorlooptijd te verkorten. Er kwam een nieuwe lakplaats, die voldoet aan de laatste milieu-eisen en tegelijkertijd verschillende machines in andere kleuren kan spuiten. Gemiddeld is de levertijd verkort met 40 %, zijn de voorraden gehalveerd terwijl de hoeveelheid mankementen is verminderd met 25 %.
(FOTO 4)
(BIJSCHRIFT)
Een assemblagelijn bij Windhof AG. (Foto: M. Verweij)
(TEKENING)
(BIJSCHRIFT)
De zes basistypen die verschillende wijzen van produceren weergeven.