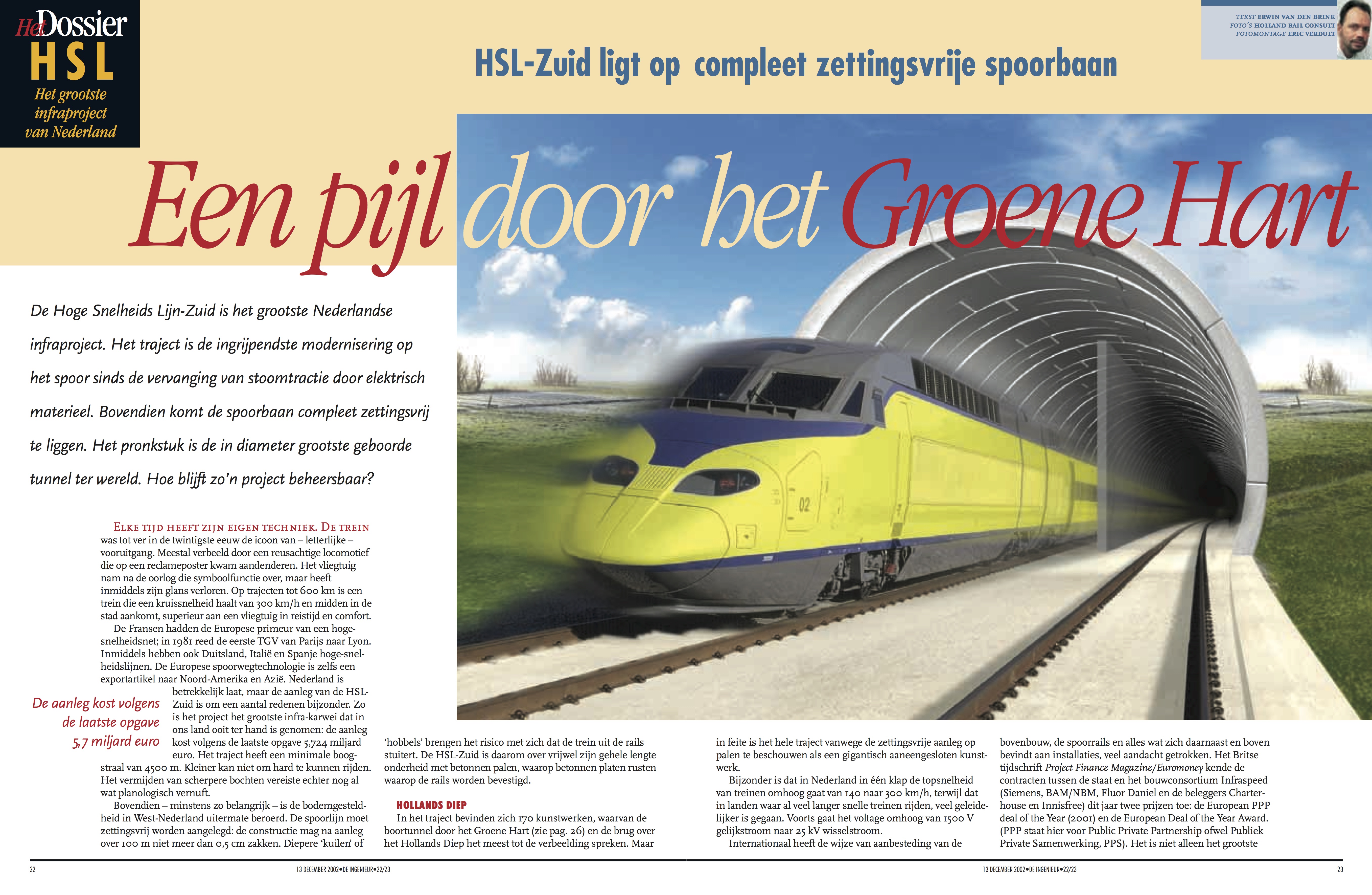
Hier klikken voor de PDF van het artikel: p22-26 Dossier_1
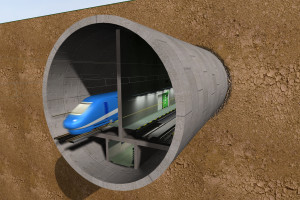
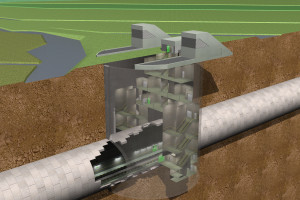
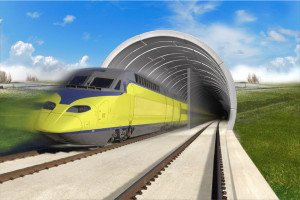

Het Dossier
HSL
Het grootste
infraproject
van Nederland
HSL-ZUID LIGT OP COMPLEET ZETTINGSVRIJE SPOORBAAN
Een pijl door het Groene Hart
De Hoge Snelheids Lijn-Zuid is het grootste Nederlandse verkeersproject ooit. Het traject is de ingrijpendste modernisering op het spoor sinds de vervanging van stoomtractie door elektrisch materieel. Bovendien komt de spoorbaan compleet zettingsvrij te liggen. Het pronkstuk is de in diameter grootste in slappe grond geboorde tunnel ter wereld. Hoe blijft zo’n project beheersbaar?
Elke tijd heeft zijn eigen techniek. De trein was tot ver in de twintigste eeuw de icoon van – letterlijke – vooruitgang. Meestal verbeeld door een reusachtige (stoom-)locomotief die op een reclameposter kwam aandenderen. Het vliegtuig nam na de oorlog die symboolfunctie over, maar heeft inmiddels zijn glans verloren. Op trajecten tot 600 km is een trein die een kruissnelheid haalt van 300 km/h en midden in de stad aankomt, superieur aan een vliegtuig in reistijd en comfort.
De Fransen hadden de Europese primeur van een hoge-snelheidsnet; in 1981 reed de eerste TGV van Parijs naar Lyon. Inmiddels hebben ook Duitsland, Italië en Spanje hoge-snelheidslijnen. De Europese spoorwegtechnologie is zelfs een exportartikel naar Noord-Amerika en Azië. Nederland is betrekkelijk laat, maar de aanleg van de HSL-Zuid is om een aantal redenen bijzonder. Zo is het project het grootste infra-karwei dat in ons land ooit ter hand is genomen: de aanleg kost volgens de laatste opgave 5,724 miljard euro. Het traject heeft een minimale boogstraal van 4500 m. Kleiner kan niet om hard te kunnen rijden. Het vermijden van scherper bochten vereiste echter nog al wat planologisch vernuft.
Bovendien – minstens zo belangrijk – is de bodemgesteldheid in West-Nederland uitermate beroerd. De spoorlijn moet zettingsvrij worden aangelegd: de constructie mag na aanleg over 100 m niet meer dan 0,5 cm zakken. Diepere ‘kuilen’ dan wel ‘hobbels’ brengen het risico met zich dat de trein uit de rails stuitert. De HSL-Zuid is daarom over vrijwel zijn gehele lengte onderheid met betonnen palen, waarop betonnen platen rusten waarop de rails worden bevestigd.
HOLLANDSCH DIEP
In het traject bevinden zich 170 kunstwerken, waarvan de boortunnel door het Groene Hart (zie pag. 26) en de brug over het Hollandsch Diep het meest tot de verbeelding spreken. Maar in feite is het hele traject vanwege de zettingsvrije aanleg op palen te beschouwen als een gigantisch aaneengesloten kunstwerk.
Bijzonder is dat in Nederland in één klap de topsnelheid van treinen omhoog gaat van 140 naar 300 km/h, terwijl dat in landen waar al veel langer snelle treinen rijden, veel geleidelijker is gegaan. Voorts gaat het voltage omhoog van 1500 V gelijkstroom naar 25 kV wisselstroom.
Internationaal heeft de wijze van aanbesteding van de bovenbouw, de spoorrails en alles wat zich daarnaast en boven bevindt aan installaties, veel aandacht getrokken. Het Britse tijdschrift Project Finance Magazine/Euromoney kende de contracten tussen de staat en het bouwconsortium Infraspeed (Siemens, BAM/NBM, Fluor Daniel en de beleggers Charterhouse en Innisfree) dit jaar twee prijzen toe: de European PPP deal of the Year (2001) en de European Deal of the Year Award. (PPP staat hier voor Public Private Partnership ofwel Publiek Private Samenwerking, PPS). Het is niet alleen het grootste PPS-contract (1,3 miljard euro) dat Nederland ooit gesloten heeft, het is tevens de grootste rail-PPS in Europa.
GARANTIE
Ir. Leendert Bouter, Hoofdingenieur Directeur (HID) van de Directie HSL-Zuid legt uit wat er zo speciaal aan is. ‘In het contract met Infraspeed is afgesproken dat de overheid niets financiert. Dat wordt door banken gedaan. Degene die bouwt, krijgt pas betaald op het moment dat het werk is opgeleverd. Dus Infraspeed is vijf jaar aan het bouwen met geleend geld van de bank. Over de opgenomen bouwkredieten rekent de bank rente die bij de schuld wordt opgeteld. Vanaf het moment van oplevering gaat de staat aan Infraspeed 25 jaar lang een jaarlijks bedrag betalen voor de beschikbaarheid van de spoorlijn. Infraspeed zal na oplevering van de bovenbouw namelijk het onderhoud van het gehele tracé (onder- en bovenbouw) , het consortium dat de bovenbouw aanlegt, zal na oplevering ook het onderhoud van de onderbouw op zich nemen. op zich nemen. Het consortium heeft zich verplicht de spoorlijn kwalitatief zo te bouwen en te onderhouden dat er 99 % van de tijd treinen veilig en comfortabel met 300 km/h over kunnen rijden. Met dat bedrag moet Infraspeed al zijn kosten dekken: de investering plus de jaarlijkse onderhoudskosten. De staat heeft de zekerheid dat zij 25 jaar lang nooit méér hoeft te betalen dan dat bedrag. Dus al het risico is vervreemd van de staat.’
Wordt die 99%-eis niet gehaald, dan gaat er een strafkorting af van de bijdrage. Bij minder dan 94 % beschikbaarheid bedraagt de strafkorting al 80 %. Die 99 % moet de staat gezekerd hebben, want zij geeft een concessie aan een vervoerder: High Speed Alliance (NS en KLM).
Bouter: ‘Als je nu kijkt naar de staatsinkomsten gedurende die vijftien jaar dat de vervoersconcessie loopt en je vergelijkt dat met de uitgaven die we gedurende 25 jaar moeten betalen aan Infraspeed, dan rest er een positief saldo. De staat heeft de onderbouw grotendeels klassiek gefinancierd a fond perdu, maar kan de investeringslasten deels dekken met het positieve exploitatiesaldo van de bovenbouw.’
Als Infraspeed met de HSL onder de beschikbaarheidsnorm duikt levert zij dus wanprestatie en daardoor zou deze private onderneming failliet kunnen gaan. Boutert acht die kans echter niet groot. ‘De kans dat de vervoerder failliet gaat is misschien groter, omdat die vaste uitgaven heeft voor de concessie, terwijl de reizigersmarkt aan schommelingen onderhevig kan zijn. Maar alles bij elkaar genomen ben ik er van overtuigd dat het goed in elkaar zit.’ Het contract met de infraprovider wordt aangeduid als Design Build Finance and Maintenance (DBFM).
BEPROEFDE TECHNIEK
Het meest spectaculaire deel van die onderbouw is natuurlijk de boortunnel, die wordt gebouwd door de combinatie Bouygues/Koop. Civiel-ingenieur ir. Hans Burger was tot voor kort manager van het Projectbureau Noordelijk Holland. Acht jaar lang was hij bij de HSL-Zuid gedetacheerd via DHV Milieu en Infrastructuur. Hij legt uit hoe Rijkswaterstaat uiteindelijk de hele engineering kon uitbesteden aan de aannemer, maar toch voldoende greep houdt op de kwaliteit en de kosten van de tunnel.
‘We hebben eerst zelf een referentie-ontwerp gemaakt met twee buizen van 9,5 m intern. Dat is beproefde techniek. We hebben toen ook wel naar een grote tunneldiameter gekeken en ook naar een Double O-Tube(DOT)tunnel, zo’n bril – dan draaien twee koppen naast en achter elkaar. Maar we wilden geen bepaalde methode voorschrijven. Echter, om vergunningen aan te vragen heb je een conceptontwerp nodig. Dus we hebben een haalbaar concept genomen: twee gescheiden tunnelbuizen. Daar hebben we zelf het hele basisontwerp van uitgewerkt om voldoende alle risico’s die aan zo’n ontwerp zitten te kennen en om kostenramingen te doen.’
‘We hebben geen kant en klaar bestek aanbesteed, maar er een echte Design & Constructaanbesteding van gemaakt, waarin veel vrijheid zit voor de aannemer. En we hebben ook uitgelegd dat het basisontwerp van ons er puur is om de aannemer te helpen: hier zie je een aanpak. Zo hebben wij het gedaan. We dagen jullie uit om met andere ontwerpen te komen en met optimalisaties, bijvoorbeeld langer doorboren. Dat betekent immers minder hinder, minder heiwerk, minder grondtransport, minder werkwegen, kortere procedures en minder bezwaren van omwonenden.’
‘We zeiden: ons inziens moet een enkele buis met een hele grote diameter ook wel mogelijk zijn in plaats van twee buizen, maar dan moet je wel aantonen dat je in staat bent zoiets te maken. Onze inschatting was dat een grotere diameter nodig zou zijn dan nu wordt gebouwd. De aannemer die met dit ontwerp is gekomen, heeft echt alles geoptimaliseerd. Hij is tot het uiterste gegaan binnen het programma van eisen en is tot een relatief kleine tunnel gekomen voor een trein die er met zo’n hoge snelheid doorheen moet kunnen.’
HEIEN
Bij de aanbesteding kon de aannemer fictieve bonussen krijgen als hij zou aantonen te kunnen zorgen voor minder omgevingshinder. Zijn aanneemsom werd dan op papier verlaagd, zodat hij dan schijnbaar lager inschreef dan de overige mededingers. Het ging om de meest aantrekkelijke aanbieding in termen van geld én milieu. Dat uitkeren van ‘bonussen’ is ook gedaan voor de aspecten ‘risico’ en ‘veiligheid’. Burger: ‘Daardoor bleek dat we beter wat langer konden doorboren. Eerst zou de boormachine (die van noord naar zuid boort, red.) vóór de dijk bij Westeinde naar boven komen. Nu gaat hij onder de dijk door tot voorbij de bebouwing en pas daarna beginnen we met cut & cover-werk waarbij je ook moet heien – waarvan de omgeving hinder ondervindt. Aan de noordkant zijn we eerder gaan boren op geringe diepte. Daar hebben we eerst de klei en het veen uit het traject weggegraven en vervangen door zandcement vanwege de vereiste stabiliteit. Dat is al met al goedkoper dan cut & cover-werk, want daarvoor zou een hele diepe bouwput nodig zijn geweest en de kosten en risico’s lopen enorm op met de diepte van de put. Langer doorboren is dus gunstig uit oogpunt van kostenoptimalisatie en risicobeperking.’
PROJECTBUREAUS
Het projectbureau HSL-Zuid van Rijkswaterstaat bevindt zich in Zoetermeer. De grote leveranciers van ingenieurs aan dit projectbureau zijn het Amersfoortse ingenieursbureau DHV en het bureau Holland Railconsult. Honderden ingenieurs zijn jarenlang zo gedetacheerd bij de projectorganisatie. Op een zeker moment waren dat er bijna duizend. Nu de bouw volop aan de gang is, zijn het er nog enkele honderden.
Ing. Wim Knopperts, afkomstig van Railinfrabeheer, is directeur project- en inframanagement en geeft leiding aan zes projectmanagers van evenzovele projectbureaus. Want voor de beheersbaarheid moest het project ‘in stukken worden geknipt’. Er is een projectbureau Noordelijk Holland dat het gedeelte bestiert van Hoofddorp tot Hazerswoude-Dorp. Vanaf daar neemt ‘Zuid Holland-Midden’ het over tot aan de noordrand van Rotterdam. In de Maasstad rijdt de Thalys als een gewone trein op 1500 V over bestaand spoor. Vanaf de zuidkant van Rotterdam tot en met de brug over het Hollandsch Diep is het bureau ‘Zuid-Holland-Zuid’ verantwoordelijk voor de bouw. Vervolgens ‘doet’ het projectbureau ‘HSL-A16’ het resterende stuk tot aan de grens samen met de verbreding van de A16 naar 2×3 rijstroken. Het vijfde projectbureau zorgt voor de aansluiting op bestaand spoor bij Hoofddorp en Breda waar de trein, evenals in Rotterdam, door zogenoemde ‘spanningssluizen’ wordt geleid van 25 kV wisselstroom naar 1500 V gelijkstroom en vice versa. De hele elektrische aandrijving is daarom dubbel uitgevoerd. Dan is er nog een apart projectbureau voor het contractmanagement met Infraspeed, de zogenoemde infraprovider, en tenslotte is er een projectbureau ‘Vervoers- en Veiligheidssystemen’ dat het contract regelt met High Speed Alliance dat de treinen gaat laten rijden.
ZETTINGSVRIJ
Bijzonder is de toepassing van systems engineering, een methodologie voor het technisch-organisatorisch beheersbaar houden van grote complexe projecten die van origine bij NASA vandaan komt en eerder opgeld deed in de vliegtuigbouw en ruimtevaart.
Bijzonder is ook het Europese No Recess-onderzoek. No Recess (‘geen zetting’) is een acroniem voor New Options for Rapid and Easy Constructions of Embankment on Soft Soil. Het gaat om het zettingsvrij aanleggen middels andere technieken dan de vertrouwde heipaal tot op het pleistocene zand. Uiteindelijk zijn de resultaten maar op kleine schaal toegepast vanwege de tijd die het kostte om ze te valideren voor grootscheepse toepassing onder het spoor zelf. Alleen ten zuiden van het riviertje de Mark zou het spoor niet zettingsvrij kunnen worden aangelegd op een conventioneel ballastbed omdat de bodem daar stabieler is dan in West-Nederland. Dat is weliswaar goedkoper, maar de ervaring elders in Europa heeft geleerd dat de onderhoudskosten aanmerkelijk hoger zijn omdat de rails regelmatig moet worden ‘rechtgelegd’. En dat betekent ook minder beschikbaarheid. Infraspeed studeert nog op de definitieve bouwmethode.
KOPSTATION
De Belgen willen dat de Nederlanders op tijd klaar zijn omdat anders hun HSL doodloopt op de Nederlandse grens. Bouter: ‘In de overeenkomst tussen België en Nederland is afgesproken: 1 juni 2005. Wij zitten inmiddels op 1 oktober 2006 voor het stuk Rotterdam-Belgische grens, dus bij elkaar vijftien maanden later. En het stuk Amsterdam-Rotterdam zou altijd al een half jaar later klaar zijn, dus niet 1 juni 2005 maar 31 december 2005 en dat staat nu op april 2007.’
‘Bij ons is die vertraging onder meer ontstaan toen de politiek ineens besloot dat de verdiepte ligging bij Bergschenhoek nog dieper moet omdat anders de hellingbanen naar het viaduct dat er overheen moet komen te steil zouden worden voor gehandicapten. Voor die diepere ligging zijn we 22 miljoen Euro extra kwijt. Omdat we op dat moment het contract met Infraspeed nog moesten sluiten dachten we er goed aan te doen om daarin alvast een voorziening te treffen voor een eventuele vertraging zodat we niet direct met allerlei claims van infraspeed zouden worden geconfronteerd indien ook werkelijk vertraging zou ontstaan.’
Al met al is tegen de HSL-Zuid minder maatschappelijke weerstand geweest dan tegen de Betuwelijn waar Bouter voorheen projectdirecteur van was. De Betuwelijn zou volgens veel bezwaarmakers doodlopen op de Duitse grens. Maar de Duitse deelstaat Noordrijn Westphalen heeft nu besloten om vanaf Emmerich de Betuwelijn door te trekken.
Er komt geen HSL-Oost waardoor Amsterdam-CS straks een eindpunt is. Maar het bestaande traject Amsterdam-Utrecht-Arnhem is een vrijwel rechte lijn – in tegenstelling tot het bestaande spoortraject door west-Nederland. Knopperts ‘Dat kan dus in principe geschikt worden gemaakt voor snellere reistijd, deels door hogere snelheden dan normaal in Nederland, deels door capaciteitsvergroting.’
Kortom, ook na de oplevering van de HSL-Zuid is het spoorwegnet nog lang niet af.
(QUOTES)
De aanleg kost volgens de laatste opgave 5,4 miljard euro
De constructie mag na aanleg over 100 m niet meer dan 0,5 cm zakken
De rails liggen elk in een goot van uitgehard epoxy
Treinen kunnen gegarandeerd 99 % van de tijd veilig en comfortabel 300 km/h rijden
(FOTO”S)
(HOOFDPLAAT – foto 107 bouwwerkzaamheden)
Bouw van de noordelijke toerit naar boortunnel met de startschacht.
(mt-06.jpg)
Doorsnede van de boortunnel.
(cam.3.jpg)
Vluchtdeur in de tunnel onder de Oude Maas.
(vanafwater.jpg)
De HSL kruist het riviertje de Mark ten noorden van Breda.
(vls-11.jpg)
De tunnel met het trappenhuis in de verticale schacht.
infraproject
van Nederland
TEKST DRS. MARCEL CROK
TEKENINGEN DR.IR. ERIC VERDULT
FOTO’S Paul Attard/Bouygues Construction
DE LANGSTE IN SLAPPE GROND GEBOORDE TUNNEL TER WERELD
Dwars door de smurrie
De grootste tunnelboormachine ter wereld boort zich een weg onder het Groene Hart. De eerste grote hobbel van de langste in slappe grond geboorde tunnel ter wereld, de passage van een van de drie vluchtschachten, is met enige vertraging door het Frans/Nederlandse consortium Bouygues/Koop genomen. Nog even en na het baggeren, het heien en het afzinken van tunnels gaat ook onze kennis van boortunnels de grens over. Hollands glorie ondergronds.
Het eerste dat opvalt bij het afdalen naar de 20 m diepe startschacht voor de Groene Harttunnel is het ontbreken van een spoorlijntje. Bij andere Nederlandse boortunnels, zoals de Tweede Heinenoordtunnel, de Botlektunnel of de Westerscheldetunnel, werden tunnelsegmenten en grout met een treintje naar de tunnelboormachine (TBM) gebracht. Het consortium Bouygues/Koop maakt echter gebruik van een train sur pneus, een trein-op-banden. Deze truck, gemaakt door Metalliance, is aan beide zijden te besturen, want keren in de tunnel kan het gevaarte niet. ‘Het achterste deel van de truck volgt exact dezelfde lijn als het voorste deel, zodat de wagen gemakkelijk van baan kan veranderen zonder iets te beschadigen’, legt Louis Ballesteros van Bouygues uit.
Die precisie is nodig, want direct nadat de TBM 2 m heeft gegraven en er een nieuwe ring van tunnelsegmenten is aangebracht, gaat het afbouwen van de tunnel verder. Eerst wordt er een betonnen kokervormige technische galerij neergezet, waarin later leidingen komen te liggen. Deze wordt aan beide zijden aangevuld met een laag stabiliserend zand. Het gewicht van koker en zand is nodig om opdrijven van de tunnel tegen te gaan. Daar bovenop komt de gewapende betonvloer waarover vanaf 2007 de hogesnelheidstrein met 300 km/h zal razen. In het midden van de tunnel storten de uitvoerders de scheidingswand die de tunnelbuis moet verdelen in twee compartimenten. Normaal vindt de afbouw van de tunnel pas plaats als het boren helemaal is afgerond. Ballesteros: ‘Om tijd te winnen beginnen wij direct aan de afbouw. Dat stelt hoge eisen aan de logistiek.’
AURORA
‘Bonjour, bonjour’, klinkt het telkens als we mannen in de tunnel tegenkomen. Frans is de voertaal voor de voornamelijk Franse en Portugese tunnelbouwers, die in een paar jaar tijd de ruim 7 km tussen Leiderdorp en Hazerswoude ondergronds mogen afleggen. Een busje brengt ons 2 km de tunnel in naar wat je het episch centrum zou kunnen noemen. De laatste 120 meter naar het voorste deel van de tunnelboormachine Aurora mogen we lopend afleggen, want zo lang is de grootste TBM ter wereld. De oordopjes die we hebben meegekregen zijn overbodig, want de TBM staat stil. Dagelijks tussen acht en twaalf uur vindt er namelijk onderhoud plaats. De resterende twintig uur werken er twee ploegen. Steeds een uur graven en een uur segmenten aanbrengen, zodat er theoretisch gesproken zo’n 18 tot 20 m per dag kan worden afgelegd.
SCHEIDINGSWAND
Ze zullen wel even met hun wenkbrauwen gefronst hebben bij Bouygues, een van de grootste bouwbedrijven ter wereld, toen ze hoorden dat die gekke Nederlanders er bijna een miljard gulden voor over hadden om een stuk weiland in tact te houden. Maar opdracht is opdracht en toen directeur Koop van het Groningse bouwbedrijf Koop Tjuchem aanklopte bij de Fransen, lag er al snel een projectvoorstel op tafel. Bouygues werkte aan de Franse zijde aan de Kanaaltunnel en heeft de afgelopen jaren meer tunnels gebouwd in slappe grond, in Frankrijk, Sydney en Hongkong. De Franse projectdirecteur Joseph Harnois legt in het naast de bouwplaats gelegen kantoor van Bouygues/Koop uit waarom zijn consortium eind 1999 werd uitgekozen. ‘Wij hebben voor de metro in Sydney ook één tunnelbuis geboord met een scheidingswand ertussen. Het voordeel is dat je in totaal minder grond hoeft te boren, dat je minder ruimte kwijt bent bij de start- en ontvangstschacht en dat je gemakkelijker en dus frequenter vluchtgangen kunt aanbrengen. Bij de Westerscheldetunnel bijvoorbeeld waren kostbare vriestechnieken nodig om de grond tussen de twee tunnelbuizen te bevriezen voordat je een dwarsverbinding kunt boren.’
Bouygues bleef daardoor met zijn offerte (940 miljoen gulden) binnen de gestelde miljard gulden. Inmiddels is dit contract overigens alweer opengebroken. De tunnel wordt duurder, omdat een aantal betrokken gemeenten strengere veiligheidseisen heeft gesteld dan het ministerie van Verkeer en Waterstaat aanvankelijk deed.
AFZINKEN
De meeste tunnels in ons land kruisen waterwegen en daarvoor is het afzinken van geprefabriceerde tunnelelementen zeer geschikt. Nederland is met een dertigtal afgezonken tunnels wereldkampioen in deze categorie. Maar Nederland wordt voller en dat versterkt de roep om niet alleen bij waterwegen ondergronds te gaan. Het Centrum voor Ondergronds Bouwen, waarin overheid, universiteiten en bedrijfsleven vertegenwoordigd zijn, groeit en groeit. Er verschijnen steeds meer ondergrondse parkeergarages en winkelcentra en een logische stap is om ook infrastructuur vaker ondergronds aan te leggen, zodat het maaiveld vrij blijft voor andere doeleinden.
Geboord wordt er internationaal al meer dan 150 jaar. De Engelsman Isambard Brunel ontwierp in 1818 al een boorschild waarmee hij later – samen met zijn zoon Marc die bijna verdronk bij een doorbraak – een tunnel boorde onder de Thames door, die nog altijd in gebruik is. Inmiddels zijn er wereldwijd duizenden tunnels geboord.
Begin jaren negentig nog wilde de Nederlandse overheid niets weten van tunnels boren in de slappe Nederlandse bodem. Minister May-Weggen veegde plannen voor een ondergrondse Betuwelijn van tafel. Het kon technisch niet vanwege de slappe bodem, aldus het ministerie, en het zou bovendien te duur zijn. Een studiereis van Grondmechanica Delft naar Japan in 1992 weerlegde de argumenten van May-Weggen. Japan heeft ook een slappe bodem, maar kent inmiddels een indrukwekkende ondergrondse infrastructuur. In 1997 startte het boortunneltijdperk in Nederland met het boren van de Tweede Heinenoordtunnel (voor fietsers en tractoren) ten zuiden van Rotterdam. Daarna werd het tempo opgevoerd. In de Betuweroute zijn drie boortunnels opgenomen, de Botlekspoortunnel, de Sophia-spoortunnel en de spoortunnel onder het Pannerdensch Kanaal. Het boren van de 6,6 km lange Westerscheldetunnel is dit jaar afgerond en Bouygues/Koop heeft inmiddels ruim 2 van de 7 km van de Groene Harttunnel geboord.
GRONDWATER
Waarom is boren in de slappe Nederlandse bodem zo moeilijk? Het antwoord is met één woord samen te vatten: water. De grondwaterspiegel ligt in grote delen van Nederland slechts 1 à 2 m onder het maaiveld. Elke kuil van enige diepte begint meteen vol te lopen met grondwater. De traditionele aanpak in Nederland voor ondergrondse constructies op land is: graaf een put die minstens zo diep is als het laagste punt van de constructie en ga daarin bouwen. Probleem is alleen dat zo’n drijvende bak een enorme opwaartse kracht ondervindt van het grondwater. Door continu het water uit de omgeving van de bouwput weg te pompen krijg je de boel droog. Vrijwel overal in Nederland is beïnvloeding van de grondwaterstand tegenwoordig echter verboden. Ingenieurs bouwen daarom dure bouwputten met vloeren van onderwaterbeton waardoor er geen beïnvloeding van de waterstand optreedt.
Bij de aanleg van de metro in Rotterdam en Amsterdam lagen straten langdurig open en moesten vele huizen verdwijnen. Het gebruik van open bouwputten (sleuven) voor tunnels onder stedelijke gebieden is anno 2002 daarom niet meer te accepteren. Onlangs is de knoop doorgehakt om de Noord-zuidlijn onder Amsterdam te boren en bij de Groene Harttunnel is ook gekozen voor boren om het landschap zoveel mogelijk te ontzien.
Bentoniet
De eerste 12 m grond onder het Groene Hart bestaat uit een zeer slappe laag klei en veen. Daaronder volgt een zandpakket van ongeveer 20 m dikte. Beneden 30/35 m NAP begint een dichte kleilaag, de laag van Kedichem. De Groene Harttunnel komt vrijwel volledig in de zandlaag te liggen. Voor het boren in niet-cohesieve grondsoorten (zand valt uit elkaar als je gaat graven) gebruiken ingenieurs de zogenaamde slurryschildmethode. Om te voorkomen dat het ontgraven gat direct weer volstroomt met grond en water, wordt de grond voor het graafwiel van de tunnelboormachine met een speciale brij, bentoniet, onder druk gehouden. Bentoniet is een mengsel van klei en water in een verhouding van 1:20. In beweging gedraagt de slurry zich als een vloeistof, waardoor transport gemakkelijk is, in rust geeft het mengsel steun aan de af te graven zandlaag. Aannemers beschouwen de samenstelling van hun bentonietmengsel als het geheim van de smid. Bouygues wil niet meer loslaten dan dat hun bentoniet wordt gekocht in Egypte. Tijdens het boorproces is maar liefst 2500 m3 bentoniet per uur nodig. Een scheidingsinstallatie bij de tunnelingang probeert zoveel mogelijk kleideeltjes terug te winnen uit het afgegraven mengsel van zand en bentoniet.
Alle boortunnels in Nederland met uitzondering van de Botlekspoortunnel zijn geboord met een slurryschild. De Botlektunnel bevindt zich in een gebied met lagen van zand, klei en veen. Vanwege de uiteenlopende bodemgesteldheid was het Earth Pressure Balance-schild (gronddrukbalansschild) geschikter om mee te boren. Ook hier is een tunnelboormachine gebruikt maar dan zonder bentoniet. Met de grond zelf en het gebruik van bijvoorbeeld schuim wordt voldoende steundruk verkregen om instorting te voorkomen.
Wereldrecord
De Groene Harttunnel is de vijfde Nederlandse tunnel die met een slurryschild wordt geboord. Uniek is wel de diameter van de door het Franse NFM Technologies gebouwde tunnelboormachine: 14,9 m. Een grotere is er in de wereld niet te vinden, alhoewel de machine voor de vierde Elbetunnel in Hamburg met een buitendiameter van 14,2 dicht in de buurt kwam. Projectdirecteur Harnois loopt ook niet zo te koop met dit wereldrecord. Hij vindt het veel belangrijker dat Bouygues als een van de weinige bouwgiganten in de wereld nog een eigen engineering afdeling heeft. Bouygues kan daarom zowel tunnelboormachines als tunnels ontwerpen en bouwen. Daarmee is het bedrijf letterlijk geknipt voor de design & construct-opdracht die de Projectorganisatie HSL-Zuid had uitgeschreven. Civiel-technisch ingenieur Robert Jan Aartsen houdt namens HSL-Zuid als uitvoeringsbegeleider het boorproces in de gaten. Wat vindt hij nou bijzonder aan de Groene Harttunnel? ‘Uniek in dit project zijn de diameter van de tunnelbuis, de logistiek en de passage van de TBM door de drie tunnelschachten. De logistiek is een opgave omdat er continu grote hoeveelheden materiaal naar de TBM gebracht moeten worden, terwijl daarachter de tunnel direct wordt afgebouwd. Elke ring in de tunnel bestaat uit tien 2 m brede tunnelsegmenten, negen grote segmenten en een kleinere sluitsteen. In totaal zijn ongeveer 36 000 segmenten nodig. De grote segmenten wegen 14,5 ton. Ze worden gemaakt in het Belgische Amay in een fabriek van Bouygues en komen via Maas en Oude Rijn tot op enkele kilometers van de startschacht. Vandaar gaat het per vrachtwagen verder, twee segmenten per ritje. In de tunnel passen zes segmenten op een trein-op-banden. Bij de TBM worden de segmenten in de juiste volgorde opgepakt en op een transportband gezet waarna de erector de segmenten een voor een met een vacuümsysteem oppakt en op de gewenste positie in de ring plaatst. Daarnaast moet er per tunnelring 20 kuub grout naar de TBM worden getransporteerd. Met grout wordt de ruimte gevuld tussen de stalen ring van de TBM en de buitenkant van de tunnelring. Ondertussen moet de afbouw van de tunnel gewoon doorgaan. Vlak achter de TBM moeten de kokervormige galerijen neergezet worden en aan beide zijden worden aangevuld met een laag gestabiliseerd zand. Dichtbij de startschacht duurt het transport niet lang, maar straks als de tunnel bijna klaar is zijn de transportwagens een half uur bezig om bij de TBM te komen. De grote logistieke uitdaging staat Bouygues nog te wachten.’
Franse school
Het gebruik van prefab tunnelsegmenten is standaard bij TBM’s. Toch kijken de Nederlandse ingenieurs met belangstelling toe hoe de Franse segmenten van hogesterktebeton (B 62,5) het houden. De andere Nederlandse tunnels zijn gebouwd met Duitse partners. De Duitsers hebben een andere filosofie bij zowel het bouwen als het installeren van de segmenten. Die aanpak is historisch gegroeid, ontdekte ir. Kees Blom tijdens zijn promotieonderzoek aan de TU Delft. Blom werkt voor Holland Railconsult (HR), maar op kosten van HR, TNO en Rijkswaterstaat mocht hij wat meer fundamenteel in het ontwerp van tunnels duiken. Blom: ‘De Duitsers gebruiken zogenaamde nok-holteverbindingen. Het ene segment heeft een uitsteeksel, het volgende segment een holte waarin het uitsteeksel past. Het voordeel van zo’n verbinding is tevens zijn nadeel. De nok-holteverbinding voorkomt extreme verschuivingen van segmenten en zo mogelijk lekkages. Als de nokken gaan aanliggen, treedt er echter wel schade op aan de segmenten, wat tot extra onderhoudskosten leidt. De Franse school gebruikt vlakke profielen. De segmenten lopen daardoor minder schade op, maar het risico van grote vervormingen is groter. Dat kan beschadiging van de rubberprofielen, die het water bij de voegen moeten tegenhouden, tot gevolg hebben. ‘Na twee kilometer boren is hier overigens nog geen sprake van’, aldus Ballesteros. ‘Bij vorige tunnels hebben we gemerkt dat de nok-holteverbinding geen functie heeft. Dan kun je hem beter weglaten. Van belang is dat de segmenten met een nauwkeurigheid van 0,3 mm gemaakt worden, niet beschadigen tijdens transport en zeer nauwkeurig worden geplaatst.’
Vijzels
De tien segmenten van een ring in de Groene Harttunnel worden met behulp van negentien vijzelparen tegen de voorlaatste ring gedrukt. Door zich vervolgens af te zetten tegen de segmenten brengen de vijzels het boorschild weer in beweging voor het afgraven van de volgende 2 m. Volgens de Duitse traditie staat er een vijzelpaar op de voeg tussen twee segmenten, dan een precies in het midden van een segment, vervolgens een op de voeg, enzovoorts. De Fransen plaatsen geen vijzels op de voegen, maar een paar op een kwart en een op driekwart van de steen. Hier neigt Blom, onpartijdig in deze, licht naar de Franse school. Blom: ‘Een campingtafel op vier even lange poten staat bij het kamperen altijd scheef. Met drie staat-ie echter altijd recht. Iets dergelijks gebeurt bij het vastzetten van de segmenten. Met twee vijzelparen op een steen zijn de krachten uniform verdeeld. Met drie is dat niet het geval. Een ander nadeel van de Duitse methode is dat als twee segmenten niet helemaal op gelijke hoogte liggen, de vijzel op de voeg het ene segment meer zal belasten dan het andere. Er kan dan een holte ontstaan bij de voeg.’
Export
Amper tien jaar houdt Nederland zich nu bezig met het boren van tunnels in slappe bodem en de vraag is welke positie ons land internationaal inneemt. Blom heeft daar wel enige notie van. De aanvragen voor zijn binnenkort te verschijnen proefschrift stromen uit de hele wereld binnen. Blom: ‘Onze tunnels worden door buitenlandse bedrijven geboord. Je wilt als overheid met die partijen inhoudelijke discussies kunnen voeren, dus is de afgelopen jaren veel onderzoek gedaan. Ook vrij fundamenteel onderzoek. Wat blijkt dan? Die bedrijven boren al zo lang met succes tunnels dat veel fundamentele vragen helemaal niet meer gesteld worden. Er is bijvoorbeeld een soort wet die zegt dat de diameter van de tunnel gedeeld door 21 de dikte van de segmenten oplevert. In formule: D/21 = dikte segment. Bedrijven hanteren die formule voor de gebruiksfase van de tunnel. Een van de verrassende resultaten uit mijn onderzoek is dat die wetmatigheid inderdaad klopt, maar niet geldt voor de gebruiksfase van de tunnel maar voor de bouwfase.’
Volgens Blom blijkt in veel gevallen de bouwfase van de tunnel maatgevend te zijn voor de dimensionering van de tunnel. ‘Japanners geven inmiddels ook toe dat ze problemen hebben in de bouwfase. Een ongewenste situatie want de bouwfase duurt slechts dagen, terwijl de tunnel daarna honderd jaar mee moet. Krachten die in de bouwfase een rol spelen, zijn onder andere de vijzels, de geïnstalleerde ringen en de groutlaag. Grout is een viscoplastisch materiaal, een soort pasta, dat de afgegraven zandlaag buiten de tunnelwand moet vervangen. Grout wordt vanuit het boorschild op vier of zes plaatsen onder druk naar buiten gebracht. Hoe de vloeibare pasta zich daar precies gedraagt, is moeilijk te voorspellen. Uit mijn onderzoek blijkt dat de groutlaag een aanzienlijke opwaartse kracht kan veroorzaken die maatgevend is tijdens de bouwfase. Een logische stap is nu om nieuwe groutsoorten te ontwikkelen of andere injectiemethoden, waardoor de belasting op de tunnelring afneemt. Uiteindelijk moet de gebruiksfase van de tunnel maatgevend worden voor de dimensionering van de tunnel. Een afnemende dikte van de segmenten levert veel geld op, want het betonwerk beslaat 30 % van alle kosten.’
(FOTO’S)
(OPENINGSPLAAT)
De tunnelboormachine in opbouw in de startschacht, najaar 2001.
(TUNNEL MET GALLERIJ)
Vlak achter de TBM wordt een kokervormige galerij neergezet, die aan beide zijden wordt aangevuld met een laag gestabiliseerd zand. De koker en het zand voorkomen dat de tunnel gaat opdrijven.
(VIJZELS)
Elk segment wordt met twee vijzelparen tegen de voorgaande tunnelring aangedrukt.
(TRAIN SUR PNEUS)
Een trein-op-banden brengt de segmenten van de startschacht naar de TBM.
(TUNNEL MET BUIZEN)
Via dikke buizen wordt per uur 2500 kuub bentonietslurry naar de TBM gebracht. Via de tweede buis gaat het mengsel van zand en bentoniet weer terug naar het bouwterrein van Bouygues/Koop, alwaar het bentoniet wordt teruggewonnen.
(ACHTHOVEN)
De 40 m diepe tunnelschacht Achthoven. Deze schacht werd tot halverwege gevuld met lagesterktebeton. De TBM heeft zich vervolgens een weg geboord door dit beton.
(BRIEVENBUS)
De ingenieurs van Bouygues/Koop hadden een spleet aangebracht in de betonnen prop (zie tekening D) in de tunnelschacht. Dit maakte het mogelijk om onder atmosferische omstandigheden onderhoud te plegen aan de boorkop.
(KADER EEN + TEKENING SCHACHT E. VERDULT)
ELEGANTE KOPPELING VAN TUNNEL EN SCHACHT
Het meest kritieke onderdeel tijdens het boren van de Groene Harttunnel, geeft ook patron Harnois toe, is het passeren van de drie onderhouds-, vlucht- en luchtschachten. Deze naar hun locatie vernoemde tunnelschachten Achthoven, (rijksweg) N11 en Bent staan op respectievelijk 2, 4 en 6 km van de startschacht. Achthoven is net door de TBM gepasseerd, maar dat ging niet zonder slag of stoot. De TBM stond drie maanden geparkeerd, voordat de tunnelschacht letterlijk voldoende gewicht had om de passage van de boormachine te kunnen doorstaan zonder als een champagnekurk gelanceerd te worden. De TBM boorde sneller dan verwacht. De ruwbouw van de schacht verliep trager vanwege een gewijzigd ontwerp.
De koppeling van tunnel en tunnelschachten is elegant en niet eerder gebruikt. Eerst graaft het consortium, na het aanbrengen van diepwanden, een groot rond gat met een diameter van 30 m en een diepte van 40 m. Dat gat wordt onder water weer half volgestort met eerst een betonvloer (B30) en daar bovenop een laag lagesterktebeton (B5). Door die laag beton mag de TBM zich dan een weg boren. ‘Probleem is alleen dat die betonnen schacht niet verankerd is aan de omringende grond met bijvoorbeeld palen en dus drijft in het pakket van veen, zand en klei’, zegt ing. Stef Slingerland van de Projectorganisatie HSL-Zuid. ‘Het is moeilijk om die grote dobber op zijn plek te houden terwijl de TBM grote krachten op de betonnen prop uitoefent.’
Daarnaast had Bouygues een soort brievenbus in het lagesterktebeton aangebracht. Die gleuf maakt het mogelijk om tijdens de passage van de TBM onder atmosferische omstandigheden onderhoud aan de boorkop te plegen. Een aantrekkelijk vooruitzicht want normaal moeten duikers de boortanden inspecteren onder moeilijke omstandigheden. Slingerland: ‘De schacht was eerst tot vlak onder de rand gevuld met water om voldoende gewicht te zetten tegenover de opwaartse kracht uit de omringende grond. Voor de inspectie moet de schacht echter droog gepompt worden en tegelijkertijd neemt het gewicht van de betonnen prop af door het graven van de TBM. Op het meest kritische punt was er slechts een verschil van 2 % tussen de opwaartse en neerwaartse krachten. Een ander risico was dat er door het verschil in stijfheden tijdens de passage van de TBM vervormingen en lekkages zouden kunnen ontstaan.’
Het oorspronkelijke plan van het consortium was te riskant, vond zowel de aannemer als de Projectorganisatie. ‘We hebben toen besloten om eerst de constructieve wanden en de muren van de trappenhuizen en ventilatieschachten verder af te bouwen voordat de TBM bij de schacht zou arriveren.’
(KADER 2 + foto segmenten + nog een klein tekeningetje van Eric)
TBM BLIJFT MET LASER IN POSITIE
Hoe vindt een tunnelboormachine zijn juiste route onder de grond? Buiten de tunnel is met GPS nauwkeurig de coördinaten van de startschacht te bepalen. Binnen de tunnel wordt met behulp van een laseropstelling die om de paar 100 m aan het plafond van de tunnel bevestigd is de exacte positie van de tunnel bepaald. Deze ontvangers registreren ook in welke mate de tunnel beweegt.
De TBM beweegt zich voort door zich met behulp van in totaal 38 vijzels af te zetten tegen de randen van de reeds gemaakte tunnelwand. Door de druk van de vijzels op de al geplaatste tunnelring te variëren – bijvoorbeeld links iets meer dan rechts – kan de boorkop ook in horizontale of verticale richting worden gestuurd. Bij het plaatsen van een tunnelwandsegment worden alleen die vijzels ingetrokken die zich ter plaatse van dat segment bevinden. De overige vijzels houden de druk op de voorgaande ring.
Om bochten te kunnen maken is een tunnelring overigens niet recht. De breedste kant van de ring is 2,02 m breed, de smalste kant 1,98 m. Door bijvoorbeeld de breedste kant helemaal boven in de tunnel te houden gaat de tunnel recht naar beneden. Alle tien segmenten zijn dus enigszins taps. Het is echter niet zo dat gestuurd kan worden met de segmenten. De tunnel volgt altijd de boorkop. De oriëntatie van een tunnelring ligt vast met de positie van het eerste segment. De overige negen segmenten worden om en om aan weerszijden van dit eerste segment geplaatst.
(foto segmenten)
De tunnelwandsegmenten in een loods; tien segmenten vormen een tunnelring.
(DERDE KADER met TABEL OVERZICHT BOORTUNNELS, ZIE EXCEL-BESTAND)
Boortunnels in Nederland
In Nederland is pas in 1997 een begin gemaakt met het boren van tunnels. De meeste tunnels zijn geboord met de slurryschildmethode, waarbij bentoniet als steunvloeistof dient om de grond voor het boorschild stabiel te houden. Deze boormethode is net als de gronddrukbalansmethode (Earth Pressure Balance) discontinu. Na 1,5 m of meer boren wordt de boormachine stilgezet, waarna een voor een de geprefabriceerde betonnen tunnelsegmenten worden aangebracht tot er een ring is gevormd. Daarna begint het boren weer.
Deze zomer heeft het ministerie van Verkeer en Waterstaat een akkoord bereikt met de gemeente Den Haag over de aanleg van de Hubertustunnel. Deze tunnel zal waarschijnlijk volgens een nieuw Nederlands boortunnelconcept gebouwd worden: de Industriële Tunnelbouw Methode, ofwel ITM. Daarbij vindt het complete bouwproces, inclusief het storten van beton, ondergronds plaats. De verwachting is dat dit de bouwtijd aanzienlijk kan bekorten. Of dit klopt zal uit praktijkproeven moeten blijken.
Internetbronnen
www.hslzuid.nl
www.highspeed.nl
Officiële sites van de Projectorganisatie HSL-Zuid. Op de eerste staan veel nieuwsberichten en voortgangsrapportages. De tweede is meer gericht op middelbare scholieren die een werkstuk moeten schrijven.
www.bouygues-construction.com
Site van de bouwtak van Bouygues.
www.concrete.citg.tudelft.nl/
Site van de vakgroep beton binnen de faculteit Civiele Techniek. Hebben in hun laboratorium drie ringen van de Botlektunnel staan die met vijzels van buitenaf onder druk kunnen worden gezet. Deze opstelling heeft ook internationaal de aandacht getrokken.
www.cob.nl
De verzamelplaats in Nederland op het gebied van ondergronds bouwen. Er staan uitgebreide beschrijvingen van de werking van tunnelboormachines op.
www.tunnelbuilder.com
Geeft een overzicht van lopende tunnelprojecten in de wereld.
www.herrenknecht.com
Site van een van de belangrijkste bouwers van tunnelboormachines.
(QUOTES)
‘Wij hebben voor de metro in Sydney ook één tunnelbuis met scheidingswand geboord’
Het gebruik van open bouwputten in stedelijke gebieden is niet meer te accepteren
Aannemers beschouwen de samenstelling van hun bentonietmengsel als het geheim van de smid
Uniek is de diameter van tunnelboormachine: 14,9 m
De Franse school gebruikt vlakke profielen
Er is een soort wet die zegt dat de diameter van de tunnel gedeeld door 21 de dikte van de segmenten oplevert